Until recently, my favorite salvaged material story was personal.
As an active member of Georgia Tech’s Alumni Association, I got word in 2016 that a work crew had removed four joists during renovation of the campus’ iconic Tech Tower. The joists were original heart pine from the building’s 1880s construction. So, I sought permission to pick them up.
I brought the 12-foot-long pieces of historic lumber home to my garage workshop. There had to be some way I could repurpose them.
It was just six days before the association’s annual Gold & White Gala, which includes a silent auction. So my wife, Angela, and I came up with an idea: Why not turn the joists into distinctive frames for Georgia Tech diplomas?
The four frames I made were a hit at the auction. Ever since, just before the annual event, I’ve trimmed away at my treasured stash to make more of those diploma frames. They’ve now raised more than $6,500 for the association. They’ve provided dozens of alumni with a tangible connection to our alma mater.
It turns out that Georgia Tech saw the value in 70 more joists that were pulled out for the renovation. The Institute placed them in storage. I didn’t realize then that those remaining joists would come back into my life and provide a nifty twist to the story.
A passion for salvage
Last fall, Skanska USA finished work on the Kendeda Building for Innovative Sustainable Design at Georgia Tech, which we believe is the greenest building in the Southeast. It’s on track for Living Building Challenge certification.
As a sustainability engineer for Skanska, I oversaw the vetting of much of the materials. I took a special interest in finding ways to incorporate repurposed materials. I’m proud to say that we managed to incorporate unique materials into the building’s design, support the neighboring community and divert tons of “waste” from landfills — all at the same time.
Reusing materials in both new construction and renovation has been a passion of mine for more than a decade. I believe it’s an important element for any truly green project. But material reuse remains quirky. It requires both planning and being flexible enough to jump at an opportunity — plus a little luck at the right time. It also can shower your project with significant cost savings and create a lot of the kind of value that’s difficult to measure.
As a young construction manager for Skanska, I often would see much larger troves than those four Tech Tower joists hauled off to the landfill. It wasn’t that people in the industry wanted to be wasteful. There just wasn’t a system in place to identify reusable materials, or to transport, store and resell it.
So in 2011, I joined with a handful of other young design and construction professionals in Atlanta to found the nonprofit Lifecycle Building Center, a nonprofit that captures building materials from the waste stream and directs them back into the community through reuse. Lifecycle now operates a 70,000-square-foot store just southwest of downtown. Its salvage retail store today diverts over 1 million pounds a year from landfills. Its match program for nonprofits has provided free material to over 190 organizations in our region.
It helps to have allies
Having an organization like Lifecycle to help us meet the Living Building Challenge’s Net Positive Waste Imperative was one of two key advantages for our team on the Kendeda Building. The other was being a project on a major state university campus.
Take our adventure to the Georgia Archives Building. In early 2017, the state of Georgia was preparing to tear down the 17-story modernist cube in downtown Atlanta. Because the Kendeda Building was going to be on a state campus, we were given access to the building before demolition began.
Alissa Kingsley, an architect with Lord Aeck Sargent, and I led a small group on a mission in search of salvageable material. Our scouting trip provided a perfect example of the need to be flexible and opportunistic when it comes to reusable materials.
RELATED STORY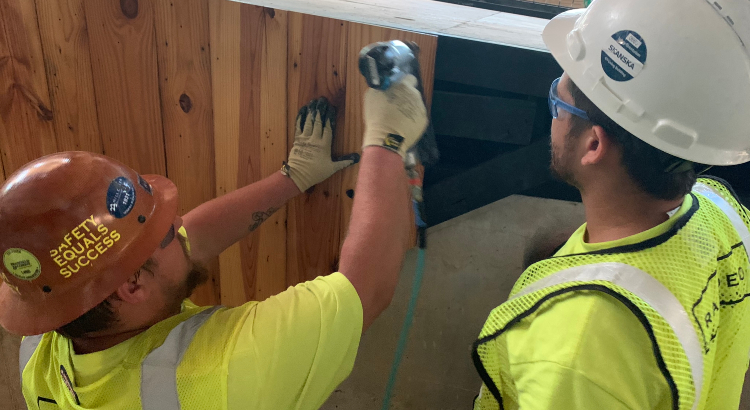
10 tips on salvage materials from Jimmy Mitchell
One of the building’s materials was on everyone’s mind beforehand. Most of the above-ground portion of the building was clad in panels of beautiful, white Georgia marble. How cool would it be to incorporate that into the Kendeda Building?
After we arrived, we pried several of those panels from the facade. What we found was disappointing: The slivers of stone had been glued to a synthetic backing during construction half a century ago. All that beautiful marble was unusable.
We could have cut our losses. Instead, we kept plodding through the dark building. We managed to remove several promising items over the next two days — just before the demolition team began setting up the building for implosion. Among them: stainless steel door pulls, exotic trim, granite curbs and exquisite mid-century modern casework.
The storage problem
Where, you might ask, did we take them? This is where Georgia Tech came through for us in another big way. The Institution agreed to set aside part of the Grinnell Building, an old warehouse on the edge of the campus, as a storage and staging area. We were even able to use this space to fabricate materials.
The fabrication operation formed the heart of our largest reuse victory. Early in the schematic design process, the team decided that weight-bearing floor panels would be created by nailing the wide surfaces of two-by-six boards together. All told, we would need tens of thousands of 10-foot-six-inch long boards to produce nearly 500 panels. Under the Living Building Challenge, all the wood had to be certified by the Forest Stewardship Council —unless the boards were salvaged. One problem: salvaged wood isn’t graded for structural purposes.
Our team came up with the idea to replace every other two-by-six with salvaged two-by-fours. The Lifecycle Building Center had a bead on thousands of two-by-fours that movie production companies dispose of every time they break down a set. The alternating depths of the boards forming the ceilings would create a lovely fluted-wood pattern. Most importantly, our structural engineers approved of the plan because the panels would still be plenty strong even with half the original number of two-by-sixes. Through a structural lens, the salvaged two-by-fours would just be spacers.
The biggest challenge turned out to be subcontractors. We discovered that none of them wanted to touch a labor-intensive contract to build structural components partly out of salvaged material. Only one company bid for the work, and the quote came in very high — about a million dollars.
Helping the community
The lack of subcontractor interest turned out to be our biggest blessing. My colleagues at Skanska and I have worked with a non-profit, GeorgiaWorks, in an underserved part of town near Georgia Tech. GeorgiaWorks provides job training to local men who are recovering from substance abuse or were recently released from prison.
We partnered with the nonprofit. Its clients helped to precisely nail those thousands of boards together. At least one of the men launched a career in the construction industry by fabricating floors with us. And the cost ended up being less than a third of that million-dollar bid.
The floor panels saved money, made the building more beautiful, helped us to better engage with the community and diverted some 25,000-linear-feet of two-by-fours from the landfill. Those movie-set two-by-fours were among about 20 salvaged materials that went into the Kendeda Building. The others included mid-century modern casework and granite curbs from the Georgia Archives.
And then there were the heart-of-pine joists from Tech Tower that Georgia Tech had put aside after seeing their value. They’ve been given new life as the treads on the irresistible staircase in the center of the Kendeda Building atrium.
I don’t want to pretend that every salvage effort is a grand slam. A lot of ideas are swings and misses – like the marble at the Georgia Archives. Even the successes take creativity, planning and patience. But when they do pan out, the results can be incredibly rewarding.
As sustainability engineer for Skanska USA, Jimmy Mitchell was a member of the project team for the Kendeda Building for Innovative Sustainable Design. PHOTO AT TOP: In 2017, Mitchell displayed lumber from fallen trees that were later milled into counters for the Kendeda Building. Photo by Ken Edelstein.