Skanska’s Jimmy Mitchell has been a strong advocate for salvaged building materials for more than a decade. His work on the Kendeda Building for Innovative Sustainable Design gave him a chance to put his experience, connections and ideas into practice. On the heels of that project, here are 10 of Mitchell’s tips for incorporating salvage materials in commercial building projects.
1. Integrate the team early
Integrated project teams are great for a lot of reasons. They’re indispensable if you want to make salvaged materials a core feature of the building. “As the contractor, we have to give [the architects and engineers] feedback,” Mitchell says. “Sometimes, we’ll hear about reusable materials because we see what’s happening on a lot of different projects.”
But there’s another advantage to involving a contractor on the integrated team during the design process: He or she is more likely to know whether installing a specific reused product will be practical. And, if contractors don’t have the answers, they’ll probably know a subcontractor who does.
2. Work with your local reuse organization
From Long Beach to Boston, a new generation of organizations has grown up around the deconstruction of buildings and the sale of reusable materials. They’re often nonprofits backed by local architects, builders and environmental groups. Their aim is to build a supply chain that puts salvaged goods on equal footing with new products and materials.
rELATED STORY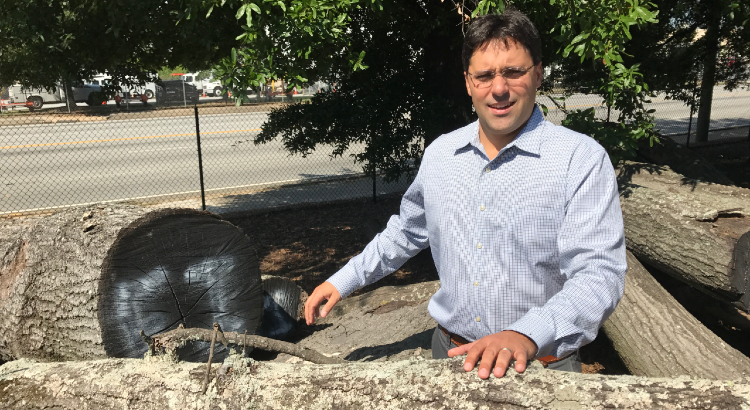
Salvaged materials tell a building’s best stories
In Atlanta, the Kendeda Building team worked closely with the Lifecycle Building Center, which Mitchell helped found in 2011. The center’s work ranged from customizing bins to store salvaged slate shingles to setting up the supply of thousands of two-by-floors to reuse in the building’s floor system.
You don’t need a similar organization in your community to make salvage a big part of your project. But it would help. Maybe, you can even rally architects and builders to start one! (Here’s a good directory of such organizations.)
3. Start looking early— and often
Even the most ordinary buildings contain materials that can be turned from trash to treasure.
“Start walking buildings that are going to be demolished, and give it a moment,” Mitchell advises. “You’re going to see things that you think are going to be good salvage products that aren’t, and other things that are going to be good but you didn’t think would be.”
Project team members can put out the word within their organizations that they’re looking for reusable materials. The owner might be renovating another property that has salvageable goodies, or the contractor might be demolishing one. Even unrelated owners might welcome tours of soon-to-be-demolished buildings because they’d be happy to know that a piece of their old building will live on elsewhere; besides, it could save them on disposal fees.
4. Collect more than you can use
“Here today, gone tomorrow” is reality in the salvage world. You must jump on good opportunities, because there’s no guarantee that you’ll ever see the same item again. Some materials just scream their possibilities; the value of others might not be obvious.
If you have a place to put the goods, cast a wide net and reel in anything that looks like a decent catch — regardless of whether you know exactly how you’ll use it. As Mitchell puts it: “If the material is available, it’s available. You just end up having to work with what you have.” Which brings up our next tip …
5. Seek a staging warehouse
The salvage and reuse process works best with patience and flexibility. Material may become available well before it can be used. So you’ll need a place to put it.
The Kendeda Building team was lucky. Georgia Tech, the owner, made an underused warehouse on the edge of campus available. The storage facility doesn’t have to be fancy or even that large, Mitchell says. “You could rope off 1,000-square-feet in an existing building.” It could be part of a garage, a storage container — anything to keep the material safe from damage or theft.
6. The schematic design phase is key
If a material is available and will be a central feature, it may be part of the original proposal. For most salvage decisions, however, the concept phase is too early. And the construction documents phase is later than ideal because reusing a material may “make you have to change the design in some way to make it fit.” So, Mitchell advises project teams to be methodical during schematic design about analyzing salvage possibilities — based on materials available and their practical applications.
In some cases, he even suggests, the architects might draw up a design set including salvaged materials and one without them, so that the team can consider the choices side-by-side.
7. Know the hurdles
Mitchell notes that salvage projects often face technical challenges that just don’t exist for new materials and products: “How do you warranty them? How do you specify them? How do you rate them?” Such questions can be crucial for structural materials, mechanical equipment, plumbing and other items that must meet regulatory standards. With a little creativity and persistence, some items can overcome such hurdles (click here for a good example). Others may just never qualify for your project.
8. Watch your bottom line
“Our mantra [on the Kendeda Building] was that none of the salvage pieces were going to cost any more money when compared to new.” Deconstruction, transportation, preservation, storage and installation can add hard expenses to a project; indirect expenses, such as design and construction delays can be even more costly. But the salvage materials themselves can cost next to nothing — or even nothing! This is a particularly big advantage on parts of green-certified projects where salvaged wood can be substituted for pricey sustainably harvested wood. Often, some steps in prepping the materials have already been taken.
It’s difficult to come up with hard-and-fast guidelines for budgeting salvage, because each use tends to be unique. The key is to keep things practical — and to anticipate unusual expenses that could get out of hand.
9. It’s often labor intensive
Salvage tends to require both low-skilled and highly skilled labor. That one reason that salvage goes hand-in-hand with the push for equity in building construction: It’s rich in entry-level positions.
10. Tell the story
Stories are part of the value of reused materials. The treads on the Kendeda Building’s grand staircase were fashioned from old joists that were taken out of Georgia Tech’s iconic Tech Tower. Two-by-fours in the floor system came from movie sets and helped struggling workers get entry level jobs in the construction industry.
There isn’t an owner, architect or builder who wouldn’t take pride in such stories, or a visitor who won’t take interest in them. And they’re part of a larger story — of a trend for properties to pass on to us an authentic sense of place.
Collect these stories and — whether it’s online, on a plaque or passed along to tenants — find creative ways to tell them!
PHOTO AT TOP: Raydeo Enterprises employees install paneling milled from salvaged wood in the Kendeda Building. Photo by Ken Edelstein.