This is the third part of a three-part story on material conservation at the Kendeda Building for Innovative Sustainable Design construction site. Read the first installment here and the second here.
Anyone who’s thrown an aluminum can into a recycling bin knows that the task never ends.
There always will be another can. Another sheet of paper. Another glass bottle.
So it is with waste reduction for a Living Building construction site. No matter how much material planning goes into the design or how many salvage items are worked into the specs, getting to net positive waste requires a vigilance that continues until the project is complete.
The actual physical effort to conserve material on the Kendeda Building for Innovative Sustainable Design construction site will end when Skanska USA, the general contractor, turns the keys over to Georgia Tech. It began with the very first construction phase: site development.
The elevations had been designed so that much of the dirt moved about by excavators and bulldozers was retained for backfill. A large magnolia tree and a handful of crepe myrtles that had to be uprooted were chipped and used as mulch. Outdoor lamp posts (circa 1970) were hauled to a warehouse on campus, with an eye toward Georgia Tech finding a reuse for them. (As it turns out, Georgia Tech officials say the lampposts weren’t reusable so they were sent on to be recycled.)
At the same time, a Materials Work Group that was established during the design process continued to search for ways to reduce waste. One key opportunity emerged when a Skanska crew began to assemble nail-laminated floor panels for the building in a warehouse on the edge of campus.
We’ve written extensively about the floor structure. Every other board in each of the 489 panels, which measure 10-foot-six-inches by six-feet, is a two-by-four salvaged from a movie set or from a church deconstructed on the Georgia Tech campus in 2017. The other half of the wood — the portion that gives the panels the structural strength to carry concrete for the building’s radiant flooring — is composed of sustainably certified two-by-sixes.
But there was a catch — an inefficiency that may sound familiar to a lot of builders. Those two-by-six boards were a standard 12 feet long. That meant the workers had to lop 18 inches off each of them, which in turn meant that there were enough scraps to fill four large pallets, weighing in at somewhere north of 10 tons.
So what do you do with more than 10,000 foot-and-half-long two-by-sixes?
The Materials Work Group brought that problem to the attention of the architects, who came up with a nifty way to repurpose them: The design for the building’s lobby calls six “occupiable steps,” broad enough for students to lounge on as informal seating. But the material for those steps hadn’t yet been found. So the architects suggested that the leftover lumber be used to form them. They’ll be bunched together vertically, creating a unique, solid surface formed by the side-by-side ends of the boards.
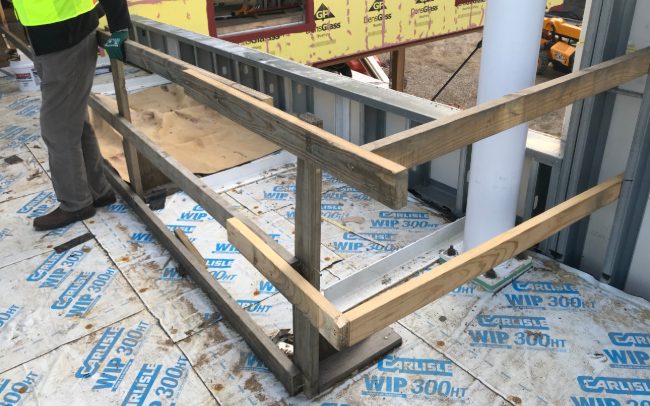
Repurposing those scraps for steps probably won’t count toward the Living Building Challenge requirement that the project include 10 salvage materials. The end pieces were generated by the Kendeda Building project, so they didn’t actually divert material from outside the project away from the landfill. At the same time, repurposing scrap wood is a much more valuable use than mulching it, so on the familiar ranking of reduce-reuse-recycling, it comes out higher.
Despite all the efforts to use soil, logs, limbs and lumber scraps, plenty of material has had to be hauled away from the Kendeda Building site. Sending materials to recyclers amounts to the last resort of the landfill.
The bulk of the material listed as recycled on the Kendeda Building project has consisted of the tons of soil that the site development contractor, Dennis Taylor and Co., hauled away during site development, along with asphalt and concrete pulled up from the parking lot that the building is replacing.
The soil is counted as recycled because it’s being used as fill. The concrete has been pounded into gravel. And the asphalt is being used to resurface an old gravel pit just south of Atlanta that’s being converted into a dump.
Since those bulk items were removed, however, recycling has become more of a small bore game. It’s consisted of hundreds of trips by individuals to the right recycling bin.
In the grand scheme of things, such intricate steps toward net positive waste may seem like quaint efforts to outrun an avalanche of garbage. Admittedly the earlier low-value bulk items — asphalt, concrete and soil — can distort the numbers. According to the December 2018 records, they alone comprised 98 percent of the recycled materials during the first 10 months of the project.
Once site development was complete, the effort became more incremental. Still, Patterson Services, an Atlanta waste management company with significant commitment to recycling, had hauled away more than 71 tons of metal, wood, paper, plastic, gypsum and tree debris for recycling. Barely, a ton of waste — one rolloff bin — had been sent to a landfill.
The system isn’t perfect — no matter how sincere the effort. Some waste may contain multiple materials, one of which can’t be recycled. Other materials don’t always fit neatly into a particular category of recyclables. In some cases, it’s difficult to tell whether the material, in the end, truly will be recycled. In one reminder that market distortions still make it too easy to landfill materials with value, the project team hasn’t yet found a nearby recycling facility that accepts rigid foam insulation.
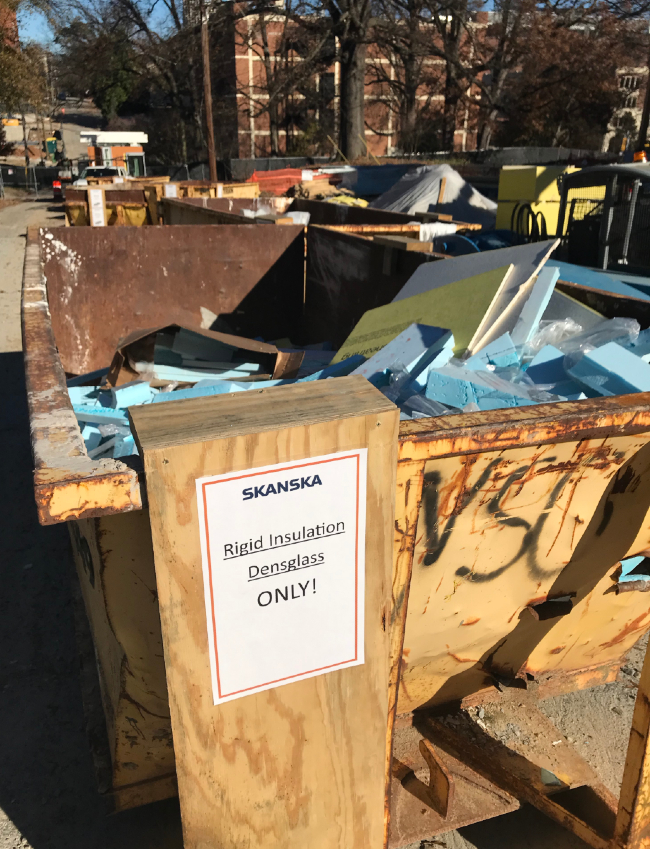
The recycling effort involves a lot of sorting and tracking. As Skanska USA Project Manager Matthew Williams puts it: “More dumpsters and more types of recyclables mean more things you have to keep up with.”
An ever-changing cast of subcontractors and their employees must get used to a different way of doing things. While many construction sites now feature one bin for waste and another for co-mingled recycling, workers on the Kendeda Building site have to get used to distributing materials into either recycling bins for gypsum, metals, paper, insulation and wood, or the waste bin.
Williams’ colleague Jimmy Mitchell offers up a long exhale when he recounts such challenges. Net positive waste can be difficult and even frustrating.
At the same time, Mitchell notes that getting used to doing things differently is sort of the point. The aim is to “bend the curve” — rather than to reinvent the entire process, and the hope is that some of the unconventional ideas adopted in Living Building projects will be replicated on enough future building projects to have a meaningful impact.
“Eventually maybe this is the way everyone will do it,” says Mitchell, who’s shepherded the project’s Materials Conservation Management Plan through various stages.
So far so good with that plan’s implementation. After 10 months of construction, hauling records showed that 99.96 percent of the tonnage removed from the site qualified as “recycled material.” With barely a ton of waste hauled to the landfill and more salvage material added to the building as the finishes are put in place, the project seems well on its way to net positive.
“The whole idea is to change the way people are thinking about materials,” Mitchell said. “This is just one project, but if it can have an impact on a big institution or big company, that’s positive. That’s change right there.”