Skanska USA is putting the petal to metal as the general contractor prepares to turn the keys over to Georgia Tech for one of the world’s greenest educational buildings.
Take the 18-hour day that kicked off last week for Jimmy Mitchell and his colleague Matt Williams.
“We get in at 5:30 in the morning to open up the site and get everybody working at six.” said Mitchell, one of Skanska’s key people on the project. “And then the opportunity presents itself at around 4 [p.m.] that we can finish [an interior air quality] test if we stay until 11:30 [p.m.]. And we say to each other, ‘Yeah, let’s stay. Let’s get finished and knock out this milestone.’ … Then, we come back this morning and start it up again. It’s kind of a wild time.”
It has been a challenging journey. Georgia Tech announced in September 2015 that the Kendeda Fund (publisher of this blog) had granted $30 million to the university to build a 42,000-square-foot building to Living Building Challenge standards, and then to operate and certify it. It would be the first building in Georgia designed and constructed under the world’s most rigorous green certification standard.
The Living Building Challenge’s goal is fairly radical: to transform the building industry into one that actually improves the environment more than it harms it. The Kendeda Fund’s objective has been to kickstart such a transformation across the Southeast.
In March 2016, a team led by architects Lord Aeck Sargent in Atlanta and The Miller Hull Partnership in Seattle won an “ideas competition” to design the building, which will look out over the campus’ Eco-Commons, a soon-to-be-restored landscape. That September, Georgia Tech announced that Skanska would serve as construction manager.
A series of charrettes and workshops followed — replete with education about regenerative design and construction. Among the sessions were a workshop on biophilic design, and various gatherings to come up with ways to meet and perhaps exceed the LBC’s Equity Petal.
It was unlike the design process for any previous building on Georgia Tech’s 400-acre campus. Forty-plus architects, mechanical engineers, landscape architects, structural engineers, contractors, consultants, university administrators, facility managers and other specialists often shared the room together.
“A lot of our projects use integrated design. But this was different. Everything was much more integrated and collaborative,” Georgia Tech Senior Project Manager John DuConge recalled this week. “I’ll give you one way to think about it. We believe we do a particularly good job of getting teams to integrate landscape design and mechanical systems into the architecture. With this project, the performance requirements necessitated that we integrate a much broader range of design disciplines into the early stages of the process.”
In fall 2017, the project faced a critical moment. The Kendeda Building was completing its design process just as national construction was booming. Bids were coming in higher than expected — higher still when subcontractors were unsure about specifications that differed from the typical project. DuConge, who was tasked with overseeing the project, convened Skanska and design team leaders to figure out how to pare the budget.
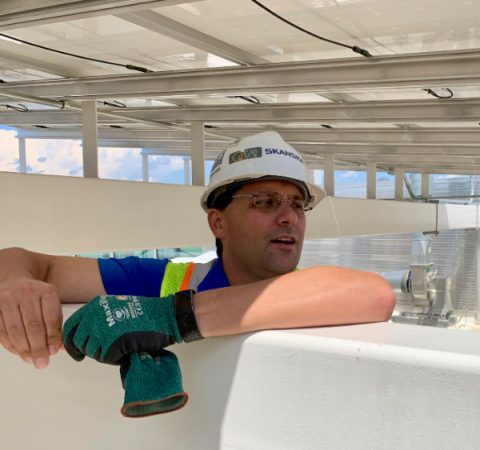
It was a painful process. Some popular ideas were jettisoned, but many of the changes actually improved sustainability measures. Clerestory windows in the atrium were downsized; even though that reduced daylighting, the height of the building was reduced to save materials and reduced systems requirements. A garage-style door between the auditorium and the atrium also was made smaller, improving the interior separations between to different HVAC systems.
The cuts also forced the design team to reduce the size of the building from 42,000 square feet to 37,000. But even that step ended up doubling down on a practice common to LBC projects: Rely on non-conditioned and outdoor spaces where possible. Even as they downsized the interior, 10,000 square feet of programmable exterior spaces were enhanced, including an outdoor classroom on the green deck over the auditorium.
Site preparation finally began in early 2018, with construction expected to take about 18 months.
“We had never done a project like this,” DuConge says. “But we benefited from the fact that we had team members with experience on Living Buildings.”
Among those LBC veterans were Chris Hellstern, a Miller Hull architect who serves as the firm’s internal expert on the Living Building projects. Hellstern stressed the need to settle on a clear process to research and select materials and products early in the design phase. That would reduce the chances that during construction hard-to-find items might arrive onsite late and cause delays.
While the early start on vetting materials helped, the fact that the Kendeda Building was the first major Living Building Challenge project in the Deep South did present supply-chain challenges. One example: The LBC requires Forest Stewardship Council certification for non-salvaged wood, but FSC lumber is difficult to procure in the Southeast. The team ended up having to contract with an upstate New York company for its glue-laminated posts and beams.
And then came the rains. Topping off above 70 inches, 2018 turned out to be the second-wettest year on record in Atlanta. 2019 started out extremely rainy as well. By the time the torrents ended, most of the construction work had moved inside.
The delays kicked back the “substantial completion” date — when Skanska turns the controls over to Georgia Tech — from an early projection of June 1 into late summer. With the punch list getting shorter, both Georgia Tech and Skanska are now anticipating that the university will take possession by mid-September.
Georgia Tech’s decision to extend a “soft opening” through the fall and to hold off on regularly scheduled classes in the building until January 2020 has provided some breathing room. Meanwhile, the building won’t be idle. More than 60 events have already been scheduled in the building this fall. Among them: A Oct. 24 building dedication, and a tour associated with the U.S. Green Building Council’s massive Greenbuild conference in November.
“There are always things you can look back at and say, ‘We could have moved faster,’” DuConge says. “Overall, though, the team did a pretty good job of keeping things moving.”
The project team plans to have loose ends such as minor electric work and punch-list items wrapped up by the time of the dedication. One challenge familiar for LBC projects became a focus earlier this month in a meeting between key stakeholders. Per Living Building requirements, The Kendeda Building must treat rainwater to supply potable water to sinks, showers and drinking fountains. The Georgia Environmental Protection Division is requiring that the building obtain its own municipal water permit, much like a utility.
Before that permit is issued, the onsite treatment system must undergo 30 days of testing and show that the treated water is safe and reliable. The test is anticipated to begin in mid-September. During the testing period, Georgia Tech will provide temporary, stand-alone sinks and water coolers. After the test, the building will use City of Atlanta water until EPD confirms that the onsite system is safe and grants the permit.
“Some of the items that need to be resolved are unusual, but [the late rush of work is] not really that different from what happens on any building. You always have these things,” Lord Aeck Sargent architect Alissa Kingsley said as she stood on the second floor, looking down on the building’s atrium. “I’m just incredibly eager to see it open.”
PHOTO AT TOP: Exterior view of the Kendeda Building for Innovative Sustainable Design from the west on Aug. 27. Photo by Ken Edelstein.