It’s been a long, hard slog. But a California startup is on the cusp of manufacturing a product that could begin a reversal in the role buildings play in climate change.
CalPlant announced in November that its new Sacramento Valley facility would soon start rolling out panels of Eureka MDF, a medium-density fiberboard composed mainly of rice straw.
As the climate crisis worsens, more urgency is being placed on steps not just to slow carbon emissions but also to reverse them. A small cadre of believers within the building industry has long pushed for buildings to become part of that solution by relying on materials that actually store carbon drawn from the atmosphere.
“If we can pull it out of the sky and put it into a building, that’s the contribution that this industry can make,” says Canadian builder Chris Magwood. ”There’s rock, soil, oceans, atmosphere and the biosphere. There are those five places where nature stores carbon. But we’re beginning to talk about buildings as being a potential sixth carbon sink.”
Magwood, who co-founded the Endeavour Centre green-building school in Ontario, may be the most prominent among a handful of small contractors who use compacted straw blocks as structural material in homes. But their movement doesn’t stop with a single construction material. Someday, they hope, buildings will reduce the amount of carbon in the atmosphere, rather than contribute to it — to a great extent by incorporating plant material into structures.
Magwood and his cohort acknowledge that the increasing popularity of mass timber is encouraging. Like agricultural waste, wood sequesters carbon. But, they argue, the short lifecycle of annual crops makes manufacturing building materials from their discards an even more efficient way to draw down carbon and to store it indefinitely within the walls of buildings.
The small straw-building branch of the green-building movement has grown more professional and come up with more standardized methods since the heyday of the Whole Earth Catalog and do-it-yourself straw-bale buildings in the 1970s. But straw has never truly scaled up. Until now.
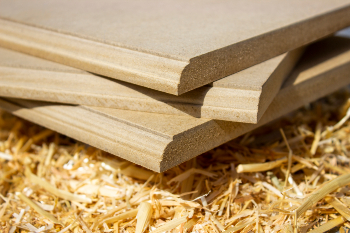
At full capacity, CalPlant — financed by more than $300 million California Green Bonds and private capital — expects annually to convert 280,000 tons of straw from the region’s vast rice harvests into construction material. That means the organic matter won’t be left to rot in standing water, where it would emit millions of pounds of methane and carbon, while also creating a wastewater challenge. And there’s plenty more rice waste where that came from.
“We brought the [factory] to the source,” says CalPlant spokeswoman Elizabeth Whalen, who’s been involved in the project during its two-decade saga from inception to completion. “The fact that we could get all the material we could possibly need within 25 miles of the plant — that changes the entire calculus.”
Getting to this point hasn’t been easy. Rice industry veterans Jerry Uhland and Jim Boyd founded CalPlant’s precursor in 1996. When they finally were ready to raise capital, the 2007 financial crisis hit. Even after the Great Recession, backing for the novel product continued to prove difficult. But in 2017 the California Pollution Control Financing Authority finally issued $235 million bonds on behalf of CalPlant. Private money followed suit, and the plant’s design was completed. But in the midst of construction, coronavirus hit, forcing a critical engineering team from the machinery company Siempelkamp to return to Germany. As if that weren’t enough, last year’s ultra-dry August, which brought hundreds of wildfires to northern California, sparked a damaging haybale fire on the CalPlant property. And the construction delays have led to bond defaults and missed payments to contractors.
Now, Whalen insists, the plant is within a weeks of beginning its commercial production run. If EurekaMDF performs well in the marketplace, investors — and competitors — may take a closer at similar efforts to convert crop waste into building products.
Globally, other ventures are at various stages. In Thailand, a self-described social enterprise called Kokoboard has fabricated particleboard from coconut fiber. Slovakia-based Ecoconon produces structural-insulating panels, mainly out of wheat straw; its products have been used in houses and small commercial construction across Europe. And early last year, Siempelkamp, which is one of CalPlant’s investors, signed a contract to build a similar rice-straw-to-MDF plant in Egypt.
None of the earlier North American efforts approach the scale of CalPlant. But it’s not difficult to imagine an entire network of carbon-sequestering building-material factories springing up across North America — each of them locking into buildings for generations millions of tons of carbon that their region’s crops naturally pull out of the atmosphere. Peanut husks in Georgia. Corn stalks in Iowa. Wheat straw in Saskatchewan. Soy pulp in Illinois. Cotton plants in Texas. And so on.
Each type of straw and each market would present challenges, Whalen acknowledges. Now, however, there’s one partnership between farmers and the building sector that could lay out a path for others to follow.
“That’s the wonderful thing about something like this,” she adds. “It stimulates innovation.”
PHOTO AT TOP: Combines harvest rice stalks in California’s Sacramento Valley for use in CalPlant’s straw-board factory. Photo courtesy CalPlant.