Upon completion of the Kendeda Building, we asked seven team members to reflect on their work on a complex Living Building Challenge project. As a lens, they used the LBC’s seven Petals. Check out all the Petal Columns by clicking here.
The centerpiece of the Energy Petal may be the Living Building Challenge’s most straightforward requirement: “One hundred and five percent of the project’s energy needs must be supplied by on-site renewable energy on a net annual basis, without the use of on-site combustion.”
Given a large enough solar array and plenty of battery storage, nearly any building could attain that ambitious goal. But addressing the LBC’s Net Positive Energy Imperative’s problem by simply throwing solar panels on the roof wouldn’t be the best use of money or other resources. The key is solid — but creative — engineering.
The Kendeda Building for Innovative Sustainable Design is the first Living Building project I’ve worked on and the first for my employer, Newcomb & Boyd, which is among the Southeast’s leading mechanical engineering firms. Paired on the project with PAE Consulting Engineers, a Portland firm that helped to design the famous Bullitt Center, we were fortunate to serve on the frontline in the rigorous certification program’s expansion into the Southeast’s hot-humid climate.
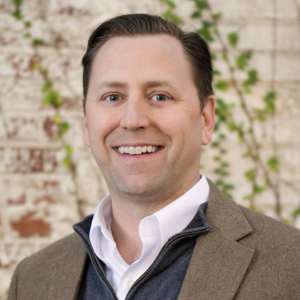
For the most part, we found that the LBC’s high standards, while tough, aren’t mystical. At a technical level, the lessons we learned reinforced the principles we’ve embraced for other high-efficiency buildings. One big difference is that positive energy is an “imperative” in the Living Building Challenge. That forces the design team to put all solutions on the table.
The first step toward net positive energy is to reduce the building’s demand across the board. Achieving that requires an integrative approach to design, since a demand reduction in one area often can create fresh demand in another. A good example of this is building lighting – how do we daylight the space without letting too much solar heat in to increase the cooling load?
Early on, the Kendeda Building design team decided that we would approach the challenge of reducing demand by taking a close look at something that seldom comes up in the design of a conventional building: We reconsidered our definition of comfort. Traditional HVAC design aims for 75 degrees Fahrenheit at 50 percent relative humidity for cooling months and 70 degrees in the heating months.
These set points were determined long ago for a typical office worker wearing business attire. But does that make sense for a typical college student? For the Kendeda Building, we widened the angle of set points to 78 degrees at 50 percent humidity for cooling and 68 degrees for heating.
At the same time, our goal was to ensure that the building would be more comfortable than any other on campus. So we turned to approaches that differ from conventional HVAC systems. Sixty-two ceiling fans in the Kendeda Building will increase air motion, and radiant floors will provide cooling and heating throughout most of the building. These two features allow for enhanced comfort outside of the typical temperature comfort range. And by extending the range, less energy is required to heat and cool the building.
With the range expanded and comfort addressed, the team searched aggressively for design features that would minimize energy loads. Shading devices were employed to maximize daylight while minimizing solar heat gain. The envelope and glazing were optimized to provide a tight and well-insulated barrier. The team even worked with the Georgia Tech on the types of coffee machines to minimize plug loads. Every effort was made to ensure that all of the necessary building functions could be accomplished by expending as little energy as possible.
A big challenge for a net positive building in the humid climate zone of Deep South was always going to involve managing moisture. In Atlanta, a significant amount of energy is often expended to cool and dehumidify, frequently resulting in the need to reheat that air to prevent overcooling of the space.
The first key to eliminating energy wasted on reheating is to decouple space cooling from dehumidification. We accomplish this by providing a dedicated outside air system. The DOAS’ primary function is to ventilate air that is cooled and dehumidified in summer and heated in winter. The amount of air delivered is proportional to the occupant load in the space. But the DOAS unit also includes an energy recovery wheel, which is a heat exchanger that can pre-cool and dehumidify hot, humid air in the summer by transferring that energy from the fresh air to the exhaust air. Likewise, it will preheat the ventilation air in the winter.
Simply segregating the ventilation air wasn’t enough to reduce our dehumidification load. So we sought additional ways to keep moisture from finding its way into the building. One innovation was our use of air curtains at every entrance. While vestibules usually provide adequate protection for moisture migration, in a heavily occupied building with large populations entering and exiting every hour, both vestibule doors figure are expected to be open for as much as 20 minutes per hour, providing a direct path for moisture to sneak in. The air curtains provided at each door combat that moisture migration, providing a barrier almost as effective as a revolving door.
The Living Building Challenge Net Positive Energy Imperative makes it clear that supply side of energy equation may not be satisfied by combustion. While natural gas or biomass can be cost-effective and relatively clean sources of fuel, they are still not as sustainable as using onsite renewable energy.
Many LBC projects choose to use electric heat pumps for their heating source. But Georgia Tech’s campus provided a unique opportunity for the Kendeda Building. Most buildings on campus are provided chilled water from one of two high-efficiency chilled-water plants — the Kendeda Building among them. However, the building also has a pair of chillers. These chillers are capable of high temperature condenser water which will provide our heat source. When operating, the chilled water they produce will be exported to the campus loop, lightening the load on the campus plants, not unlike when the buildings photovoltaic array exports excess electricity to the campus power network.
These are just some of the cool solutions we adopted in the process of meeting the high standard of the Net Positive Energy Imperative. In the early stages of design, the project challenged my assumptions of what is possible in a climate like Atlanta. As we worked through the design process, we found that solid architecture and engineering design, coupled with hyper-attention to detail, will see this project through to meeting and (hopefully) exceeding its energy goals.
Being part of the team has truly been a highlight of my career. As the systems come online, we are all very excited to start dissecting the data that will pour out of this building so we can replicate this success all over the southeast. But that’s a story for a future column.
Georgia Tech graduate Todd Mowinski, LEED AP BD&C, is a partner at Newcomb & Boyd, a mechanical and specialty engineering firm based in Atlanta. LEED Accredited Professional, Building Design + Construction. As a member of the design team, he is a mechanical engineer of record for the Kendeda Building for Innovative Sustainable Design.
PHOTO AT TOP: Hannah Solar installer works on wiring for the Kendeda Building array. Photo by Ken Edelstein.