It’s easy to see why a Canadian startup in the maritime province of Nova Scotia has emerged as a global darling for green-building venture capitalists.
CarbonCure Technologies is tackling one of the construction industry’s truly vexing issues: The astounding volume of carbon emitted during the production of cement. While the company’s technology reduces the embodied carbon of cement (and therefore concrete) by only a fraction, it’s doing so in a scalable fashion that could have a powerful impact. The company’s strategy is to install its equipment and establish its proprietary processes at hundreds of concrete plants, while at the same time developing its technology to reduce carbon emissions even more aggressively in the future.
Since its most recent dose of capital — last fall from Bill Gates’ Breakthrough Energy Ventures — the 11-year-old company has ramped up its expansion into ready-mix plants as distant as Singapore. Its overall goal is fairly audacious: To reduce carbon emissions associated with concrete by 500 million metric tons a year. (Read more in our Q&A with CEO Rob Niven.)
When ready-mix giant Thomas Concrete began pouring CarbonCure-treated concrete for its footings, the Kendeda Building for Innovative Sustainable Design at Georgia Tech became one of the first buildings in the Southeast to take advantage of the technology. And the partnership with Thomas Concrete has yielded other high profile projects: In 2017, a 12-story office tower along the Atlanta Beltline became the largest building yet to use CarbonCure, and now the CarbonCure concrete is being incorporated in a major expansion of the Georgia Aquarium.
By using CarbonCure, those three Atlanta buildings have diverted more than 2 million pounds of carbon from the atmosphere, according to the company. Last Tuesday, a ticker on its website last week claimed that 80.4 million pounds of CO2 emissions had been saved so far through CarbonCure. More than two-thirds of that had been added in the previous 365 days.
The big itch
Venture capitalists like to ask what “itch” in the market any startup proposes to “scratch.” To take the metaphor a bit further, Rob Niven’s idea was to tackle a whole-body inflammation.
The cement industry contributes a flabbergasting 7 percent to global carbon emissions, according to the International Energy Agency. That’s one-quarter to one-third of all industrial emissions. And it’s a portion that appears to be rising.
As an engineering student at McGill University in Montreal during the early 2000s, Niven began studying cement’s greenhouse-gas problem. Cement is such a large greenhouse emitter not just because of the fossil fuels used in processing its raw materials. The major factor is that huge amounts of carbon dioxide are released when one of those raw materials, limestone, is converted to lime.
The solution that Niven settled on was rather nifty: Inject carbon dioxide captured from various other industrial processes into concrete during the mixing process. A chemical reaction would “mineralize” that carbon dioxide, which would have the added benefit of making the concrete compressively stronger.
The process reduces carbon emissions from cement in two ways. It cuts the demand for cement because the CO2 displaces cement in the concrete mix. More significantly, carbon captured from elsewhere is sequestered in the concrete rather than released into the atmosphere, reducing the net emissions.
CarbonCure’s early growth was mainly in the masonry market, where companies were able to incorporate the process into standard mixes without dealing with too many variables. Since 2016, however, the company has been scaling up by contracting with ready-mix producers like Thomas.
An offer they can’t refuse
From a ready-mix company’s perspective, the business case for CarbonCure is fairly irresistible. The company installs a storage tank, hoses and monitoring equipment at the mixing plant, trains the plant’s workers, and supplies the carbon dioxide in liquified form. And
“We have seen no downsides to using CarbonCure,” Drew Millwood, the Thomas Concrete technician who oversaw the Kendeda job, wrote to me in an email. “It allows for cement reduction in any mix it is used in and provides strength at or above design. No cost increase is involved in a mix containing CO2 as the savings from cement reduction offset the cost of CO2 delivery. Equipment costs are easily recouped due to the savings.”
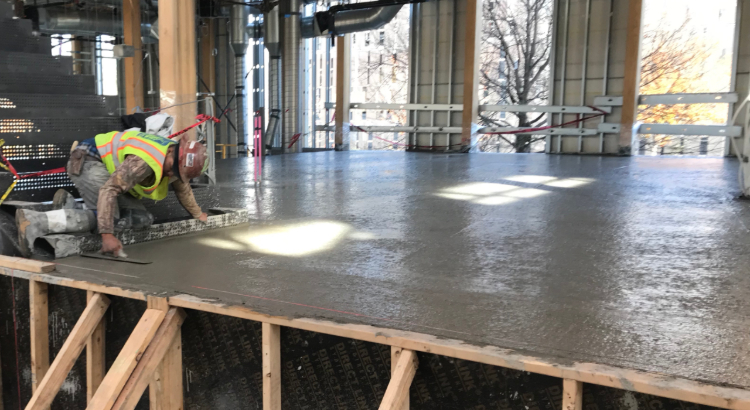
Another advantage: The ready-mix multinational begins to get its arms around a challenge that’s sure to get more formidable as the industry faces increasing pressure to deal with its carbon emissions problem. Of the nearly 150 concrete plants now using CarbonCure in North America and now Asia, 25 are operated by Thomas Concrete. The company’s early adoption of CarbonCure and its use of it in the Kendeda Building recently earned Thomas Concrete a Changemaker Award from the Kendeda Building Swarm.
CarbonCure itself, meanwhile, continues to draw international attention. For four years running, the company has made been ranked as among the Cleantech 100, a prestigious list of innovative private companies worldwide. Breakthrough Energy Ventures’ investment followed at least five other rounds of venture capital. And CarbonCure is one of just 10 finalists worldwide for the $20 million NRG COSIA Carbon XPRIZE.
In the real world, CarbonCure’s impact appears to be growing: Today, CarbonCure’s website ticker had kicked up to 81.4 million pounds. That’s still a very long way from 500 million metric tons a year … but it’s a million pounds closer than last week.
Product basics: CarbonCure
Company: CarbonCure is based in Halifax, Nova Scotia, and employs approximately 30 people. The privately held company doesn’t disclose its financing, but it has raised at least five rounds of venture capital.
Kendeda Building supplier: Thomas Concrete, whose 25 U.S. plants use CarbonCure technology.
Kendeda Building subcontractor: Greater Georgia Concrete LLC.
How it works: The company has contracted with ready-mix companies that operate more than 100 plants in the Canada, Singapore and the United States. CarbonCure installs a holding tank and other equipment at those plants, and supplies the tank with carbon-dioxide in a liquified state. Plant workers add the CO2 to the ready-mix batch, where it reacts with the lime and other ingredients to re-mineralize. Because minerals are formed at the molecular level, the carbon is locked concrete and cannot be released again even if the concrete is pulverized. CarbonCure also is used in 21 plants that manufacture concrete masonry and pre-cast products.
Sustainability features: CarbonCure reduces the carbon emissions embodied in concrete installations in two ways. By capturing and mineralizing carbon emitted in separate industrial processes, it sequesters those emissions, preventing them from getting into the atmosphere. Then, at the ready-mix concrete plant, when the material is injected into the mix, it supplants a portion of carbon-intensive cement. The net reduction in carbon emissions associated with ready-mix concrete currently is around 5 percent. but the company’s game plan is to progressively increase the reductions by further developing its technology.
Competing technologies: Other companies haven’t had as much of an impact on the market yet, but some are in production already and share aggressive goals. It should be noted that these companies may be competing in some areas (for capital, for instance) but many of the approaches may turn out to be complementary to each other.
- Silicon Valley startup Blue Planet is using captured CO2 to form a synthetic “limestone” coating around stone that can be used as aggregate in concrete mix. The company expects to open a production plant within a year in California — the first of many that its founder hopes will supply aggregate around the world.
- New Jersey-based Solidia says its method, which replaces water with CO2 in the concrete mix and then adds more CO2 during the curing, capable of reducing the carbon embodied in pre-cast products by 70 percent.
- CarbiCrete, based in Montreal, touts its “cement-free” technology as “carbon negative.” The process uses industrial slag instead of cement in addition to injecting captured CO2 into the concrete mix. Like CarbonCure, CarbiCrete has roots at McGill University; also like CabonCure, the company is one of 10 global finalists for the $20-million NRG COSIA Carbon XPrize.
- HeidelbergCement Group, a German multinational, is constructing a carbon-neutral cement plant in Breven, Norway. The plant will use low-carbon fuels. But its most notable innovation is to capture emissions, and then to extract, compress and store the CO2.
PHOTO AT TOP: Thomas Concrete ready-mix, treated with CarbonCure, pours out of a truck at the Kendeda Building Site. Photo by Vertical River.