Early on the morning after Christmas, subcontractors were stirring throughout the Kendeda Building for Innovative Sustainable Design. They were getting ready for a complicated concrete pour that none of them had ever undertaken before.
“Everybody got out here at 6:30 a.m., and it turns out that there were so many little things to take care of,” says Skanska Project Engineer Jimmy Mitchell.
The 50-cubic-yard pour, across part of the building’s first floor, was the first of five in which a thin layer of a special, fiber-heavy concrete is being spread over tubing for the building’s radiant floors. The first floor is now complete. The second floor will be poured in February.
Mike Snider led a small crew from mechanical plumbing sub Batchelor & Kimball Inc., who were there to ensure that the cross-linked polyethylene (PEX) tubing they’d carefully laid out across a layer of foam insulation wasn’t damaged or jostled out of place while the concrete was poured over it.
A technician from Johnson Controls also arrived in the morning to lay down sensors, which will ensure that the concrete flooring that encases the tubes holds precisely the right temperatures to heat or cool the spaces above.
And, of course, Greater Georgia Concrete was there to pour the concrete itself, then to float it and finally to cut control joints.
“This stuff moves a lot slower,” Greater Georgia Assistant Superintendent Brandon McDaniel said after about seven hours of working with it. “Fifty [cubic] yards will usually take about an hour [or] an hour-and-a-half to spread. This took more than four hours.”
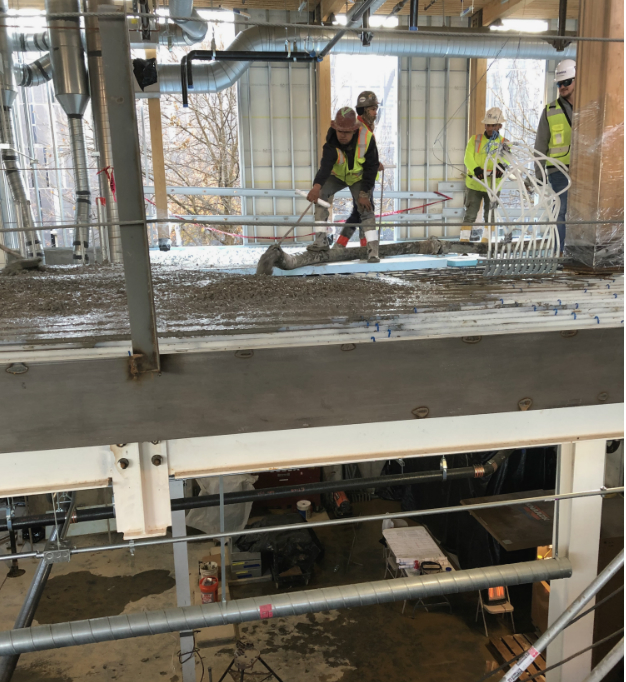
The concrete being used for the radiant floors is even more unique than the concrete that Greater Georgia poured last summer for the building’s footings and foundation. Like that mix, this one was injected with CarbonCure — an additive that increases the carbon content in the cement, both to strengthen the cured concrete and to mitigate the carbon emitted from cement during the manufacturing process.
That’s not what made this pour more complicated than usual, however. The mix for the flooring also includes a healthy helping (7.5 pounds per cubic yard, to be exact) of synthetic fiber additive called Forta-Ferro, which is intended to prevent the thin layer that will cover the PEX tubing from cracking. More important from a structural standpoint, the fiber additive allows the building to rely on thinner layer of concrete, which means the structural engineers from Uzon+Case in Atlanta didn’t have to design wood posts, beams and wooden floor panels to support quite as much weight as they otherwise would have had to.
After the day-after-Christmas pour, the concrete crew essentially followed BKI as the mechanical and plumbing contractor laid out the tubing. The radiant floors are now fully installed, leaving them only to be finished with a polish.
Mechanical engineers at PAE in Portland, Oregon, and Newcomb & Boyd in Atlanta decided to rely on a radiant system throughout the entire Kendeda Building. The only exception is the building’s auditorium, where they opted for a more conventional forced-air system — better suited to quick changes of the number of occupants.
It takes more time to heat and cool a space by heating or cooling its concrete floor, but that radiant system is far more efficient. Among the reasons: it transmits the heat without requiring fans that move large volumes of air. Additionally, the temperature changes take place at floor level where the people are — which means that energy isn’t wasted on conditioning the ceiling of each room. Read more about the Kendeda Building’s HVAC system here.
PHOTO AT TOP: Detail shows the radiant floor’s insulation layer, PEX tubing and concrete. Fortified with synthetic fiber, the concrete mix proved difficult to spread but is strong enough to reduce as amount concrete needed. Photo by Jimmy Mitchell.
That is pretty neat to see that the flooring for the radiant is different than the other concrete used. I would assume it would be because of the radiant? Then again, you did mention that the concrete does have an added layer of synthetic fiber to help prevent the pex tubing from cracking.
That wasn’t among the reasons cited to me, but I will check.
Thank you for your valuable resources keep share the information like this…
This is some pretty new concrete work they were working on. We’ve yet to lay concrete over heated tubing. Maybe one of these days we’ll get a request for it. Thanks for the writeup, it was interesting.